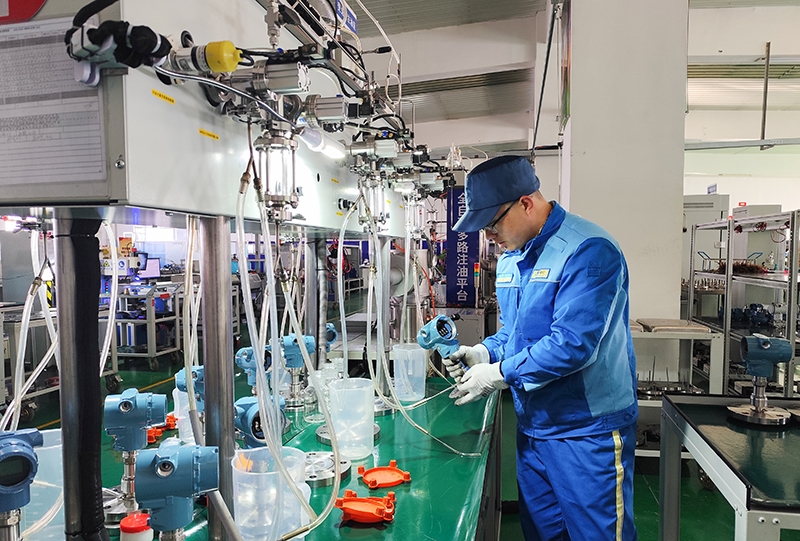
今年以來,魯西集團不斷深化全面、全過程成本管理要求,堅持“一切成本費用皆可控”的原則,從提高全員成本意識入手,扎實推進各項降本增效活動。電器儀表公司認真落實降本增效工作要求,廣大干部員工充分發(fā)揮主人翁精神,立足崗位深挖潛,精打細算降成本,斤斤計較增效益,“節(jié)”盡所能為企業(yè)發(fā)展做貢獻。
走進配電柜組裝工序,可以看到殼體組裝所需的零配件多達20余種,頂絲、接地螺釘、銅柱、接線端子、焊線……多而雜的小配件因為不起眼,經(jīng)常性的被隨意丟棄。為了避免不必要的浪費,組裝工序?qū)⑺枇闩浼?ldquo;零存整取”的形式,將零星而雜亂的小配件以成套的形式附屬在殼體上合并出庫,一對一配置,組合固定,“零存整取”為小配件“安家”。原來一個月出庫一次的零配件,變成現(xiàn)在的兩月出庫一次,每月節(jié)約螺釘至少300多個。
注油工序?qū)?ldquo;精打細算”發(fā)揮的淋漓盡致。硅油作為制作法蘭變送器的必需品,在注油方式未改進前,每一臺變送器注油量的多少,只能根據(jù)人為的經(jīng)驗去判斷,沒有確切的使用標準,這就造成了制作前對硅油進行加熱處理的用量很難把控。制作完成后剩余硅油含有雜質(zhì),不能二次使用,長此以往,造成廢舊硅油的堆積。為解決這一瓶頸,注油臺增加抽濾瓶裝置,對剩余硅油利用抽真空方式進行雜質(zhì)過濾,廢舊硅油得到了最大限度的利用。同時改進注油方式,根據(jù)毛細管的長度以及硅油密度計算出準確的注油量。3米、5米、8米……各類型毛細管法蘭變送器的注油量得到了精準把控,經(jīng)過改進后,原來每月20公斤硅油的使用量,降低到現(xiàn)在的10公斤,并且利用率至少提高了50%。
膜片焊接工序?qū)?ldquo;斤斤計較”進行到底。法蘭膜片主要有鉭、哈氏合金、鍍金等貴重金屬壓制而成。由于直徑及材質(zhì)的差異,膜片結(jié)構(gòu)的裁剪拼接過程中不可避免的會與初始設(shè)計形狀有出入,下腳料也隨之增多。焊接工序不斷進行優(yōu)化創(chuàng)新,通過測量貴重金屬板的尺寸,根據(jù)DN50、DN80、DN100膜片的直徑進行合理化排版,最大限度的做到物盡其用。小創(chuàng)新,大改善,通過嚴格控制邊角料的剩余重量。根據(jù)每月的稱重顯示,下腳料降低了20%。
“取之有度,用之有節(jié),則常足。”魯西集團干部員工從點滴做起,從細節(jié)入手,將勤儉節(jié)約之風融入到每項工作任務中,努力爭做降本增效的先進標兵。